The relentless quest to find low-carbon substitutes for conventional fossil-fuel based technologies is one of the most prolific fields of technical innovation in the world today. David Talyor interviews James Macnagten, co-founder and CEO of Caldera and Daniel Kirt, CCO.
From the search for alternative fuels such as HVO and hydrogen to attempts to reduce the massive carbon footprint of the cement industry, scientists and engineers are exploring every possibility to keep the lights on and the wheels turning without exacerbating the threat of climate change.
Renewable energy sources like wind and solar power are now established components of the energy mix. We tend to think of renewable energy in terms of electric power – and of course that is what we get from our wind and solar farms. But it is often heat that the end-user needs.
Domestic customers need heat to warm their homes and provide hot water – and since the government has decreed that no new homes can be fitted with gas boilers from next year, there has been a rapid growth in the popularity of domestic air-source heat pumps.
But industry also consumes a lot of heat energy. In fact, much of the electricity and gas consumed by manufacturers – particularly in industries such as food production and pharmaceuticals – is used to heat water and power production processes.
It is with an eye to this market that a Hampshire-based startup called Caldera has developed a type of storage boiler (also known as a “megacell”) to store energy supplied by solar panels in the form of heat.
The system consists of a solid matrix made from scrap aluminium and volcanic rock encased within a vacuum-insulated housing. Each cell can store heat at up to 500oC and deliver energy on demand in the form of hot water or steam at temperatures up to 210oC.
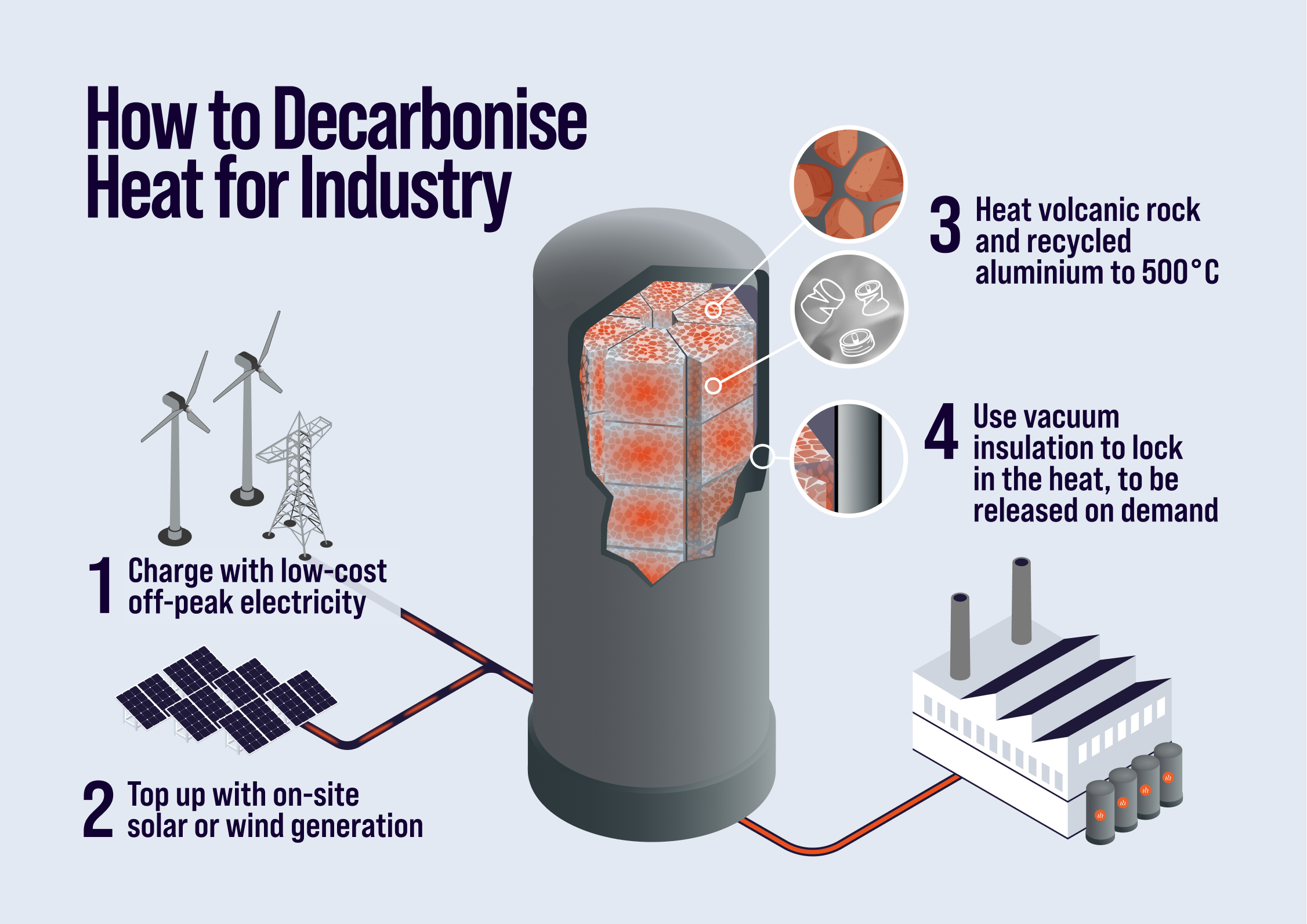
Caldera already has a small-scale demonstrator at its factory in Fareham and is now scaling up by building its first full-size storage boiler, which will be 2.9 metres in diameter, seven metres high, and capable of storing up to 4MWh of low-carbon thermal energy.
The proprietary aluminium-rock composite – described by Caldera as a ‘thermal super material’ – has been developed by the company to store low carbon electricity as heat both cheaply and effectively.
“The materials are very simple,” says Caldera’s chief commercial officer Daniel Kirk.
“We melt the aluminium (we use the lowest-grade scrap – mostly old engine blocks) and pour it over the rocks. You could make the core of the boiler entirely out of aluminium if you wanted – the rock is just a filler,” he explains.
Kirk says that one of Caldera’s aims is to produce a solution that would be easy to replicate anywhere in the world, hence the use of cheap materials.
Electricity generated by solar voltaic panels heats up the cell core via elements embedded in the matrix. The most sophisticated part of the system is the vacuum-insulated double-skinned steel enclosure surrounding the core.
“It is basically a storage heater in a vacuum flask,” says Kirk. “The problem with domestic storage heaters has always been that they let heat out whether you want it or not. Our insulated flask is very efficient and prevents significant heat loss.”
The project has £4.3m backing from the UK Department for Energy Security & Net Zero, and now company chief executive James Macnaghten is seeking industrial partners to host its large storage boilers.
This article was first published in the November 2024 issue of The Construction Index Magazine. Sign up online.
“Most people think the steam age ended last century – but in fact it has never gone away,” he says. “Around 70% of UK industrial energy demand is for heat, with industrial steam accounting for 31% of the total.
“This steam is crucial for processes in sectors like pharmaceuticals, food manufacturing and brewing and is typically generated by boilers burning gas or oil. Steam is ideal for many businesses because it holds a lot of heat which can be moved around relatively easily via pipes and valves.
“To date, most factories still rely on gas to heat that water – but our technology allows industrial users to capitalise on inexpensive solar energy which can be generated on-site or on land nearby.”
Matching the solar plant with the cell installation is a surprisingly complex procedure, says Kirk. “It depends upon a lot of factors, such as the location, the temperatures required and the level of demand.” You can’t simply prescribe a certain square-meterage of solar panel per storage boiler.
However, you do need a significant number of solar panels to feed the system. “Rooftop solar alone generally doesn’t do it,” says Kirk. “They’re usually not big enough.” In most cases, the user will need to own or rent land nearby to accommodate a dedicated solar farm.
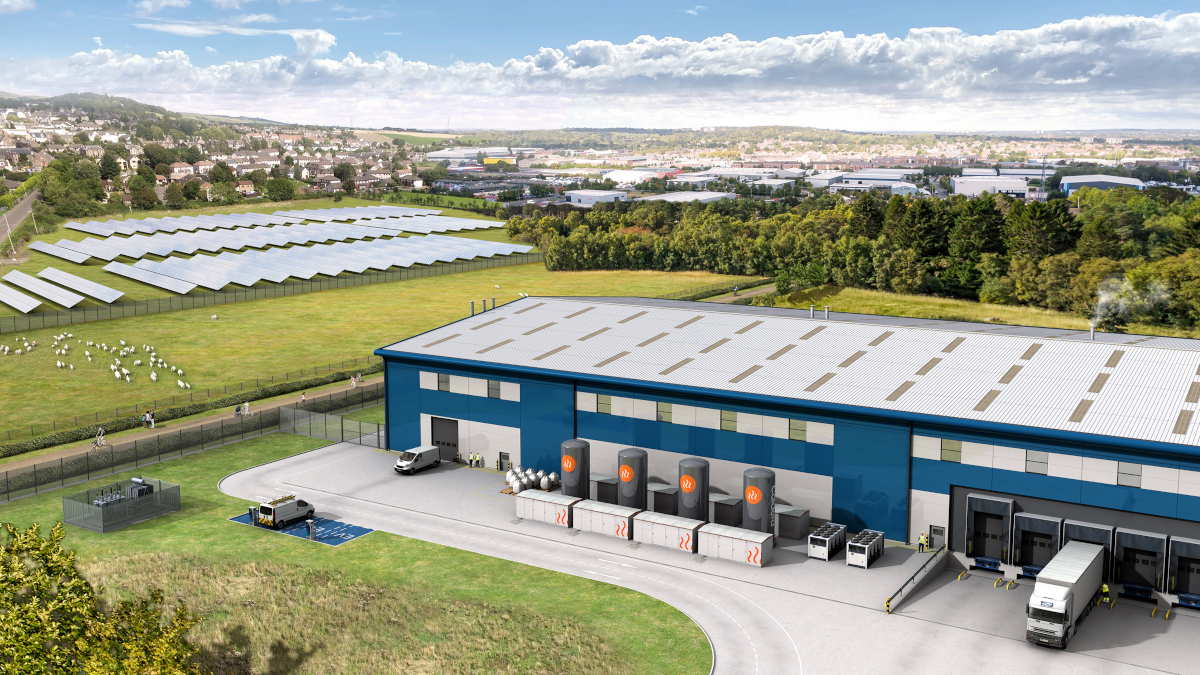
“Solar energy is getting cheaper by the day, and many businesses have not yet realised the huge potential for installing a dedicated solar farm – even where little roof space is available,” comments Macnaghten.
“It is often both feasible and economic to lease land for a solar farm in the vicinity and run a dedicated cable – known as a ‘private wire’ – for a kilometre or more to the industrial site,” he says.
“Our system removes the need for costly grid connection upgrades, which can take years, and means the factory owner can generate and use all of their solar energy at cost.
“This transforms the economics of solar power and gives the site owner price certainty over decades, allowing manufacturers to focus on their core business, and not on the price of gas.”
Analysis by energy consultant Gemserv suggests that Caldera’s system could cut fuel bills by 45% and pay for itself in less than six years.
To date, Caldera has been developing a number of small heat cells, connected in parallel, and the development of the “megacell” has come through discussions with industrial users.
“Many industrial sites have a constrained footprint. It therefore made sense for us to move away from multiple small cells to larger and much taller cells,” Macnaghten says.
The new “megacell” storage boiler is compact enough to be delivered on a normal truck but, being much taller, can store significantly more heat than its predecessors.
Having run trials of its smaller storage boilers for several months, Caldera has now commissioned a large-scale demonstrator at its facility in Fareham.
And while it is still in the testing stages, Caldera is already busy speaking to potential customers engaged in the manufacture of a variety of products including paper, agricultural products, food & drink and even building materials. They include “lots of companies you would have heard of,” teases Kirk, who says that Caldera expects to start installing its first commercial installation early next year.
Combining renewable electricity with energy-efficient heat storage is one way of supplying sustainable on-demand steam and hot water on an industrial scale; but it’s not the only way.